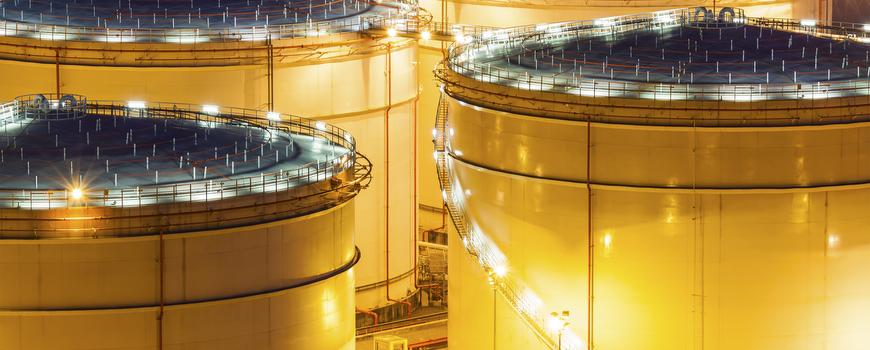
This insight summarises the key obligations on operators of sites with the potential for explosive atmospheres, as set out in EU directives 94/09/EC (replaced by 2014/34/EU) and 1999/92/EC, often referred to as the ATEX 'manufacturer' directive and the ATEX 'user' directive respectively.
ATEX manufacturer directive
Directive 94/9/EC applies to equipment and protective systems intended for use in potentially explosive atmospheres, and safety devices, controlling devices and regulating devices intended for use outside potentially explosive atmospheres but required for or contributing to the safe functioning of equipment and protective systems. This directive is frequently referred to as the ATEX 'manufacturer' directive and was transposed into Irish legislation via the European Communities (Equipment and Protective Systems Intended for use in Potentially Explosive Atmospheres) Regulations, 1999. The directive has been replaced by directive 2014/34/EU as part of the EU's New Legislative Framework (NLF). The new directive comes into effect from 20th April 2016.
Compliance with this legislation is primarily a matter for the manufacturers of equipment - there are no direct obligations on site operators. However, once appropriate hazardous area zones are specified at a site in compliance with the ATEX 'user' directive (see below), the site operator must ensure that all electrical and mechanical equipment selected for use in these zones is certified by the manufacturers to the categories set out in the ATEX 'manufacturer' directive.
ATEX user directive
Directive 1999/92/EC - the ATEX 'user' directive - is linked to the ATEX 'manufacturer' directive and sets out the minimum requirements for improving the safety and health protection of workers potentially at risk from explosive atmospheres. It is transposed in Irish legislation in Part 8 of the Safety, Health and Welfare at Work (General Application) Regulations, 2007.
An explosive atmosphere is defined as a mixture with air, under atmospheric conditions, of flammable substances in the form of gases, vapours, mists or dusts in which, after ignition has occurred, combustion spreads to the entire unburned mixture. Note that, unlike other analogous legislation (e.g. control of major accident hazards (COMAH) / Seveso), there are no minimum thresholds for inventories of dangerous substances above which the ATEX legislation applies.
As the title of the directive suggests, the primary objective of this legislation is the protection of workers from the impacts of explosions. In this regard, the principal obligations on site operators are to:
- Assess the risks arising from explosive atmospheres.
- Implement appropriate measures to protect workers from explosive atmospheres – these measures can be technical or organisational in nature.
- Classify places where explosive atmospheres may occur into appropriate hazardous area zones.
- Develop and maintain an explosion protection document.
ATEX risk assessment
A key obligation on employers under the ATEX 'user' legislation is to undertake a 'suitable and appropriate assessment' of the explosion risks at the site.
To satisfy this requirement, employers must demonstrate that explosion risks have been systematically identified at the site and that these risks have been thoroughly assessed. In undertaking this assessment employers must consider:
- The likelihood that explosive atmospheres could occur and their persistence.
- The likelihood that ignition sources, including electrostatic discharges, could be present and could become active and effective.
- The possible interactions between installations, substances and work.
- The scale of the anticipated explosion effects.
- Interconnection of areas where explosive atmospheres could occur.
- Measures to safeguard workers from explosion hazards that are already in place at the site.
- Any additional information an employer may need to complete the assessment.
Written records of the ATEX risk assessment are required.
Explosion protection measures
The ATEX 'user' legislation requires employers to take technical and organisational explosion protection measures to ensure the health and safety of workers. These measures may be grouped into three categories:
- Measures to prevent the formation of explosive atmospheres.
- Measures to prevent sources of ignition in areas with potential explosive atmospheres.
- Measures to mitigate the impacts of explosions.
As well as taking due regard of existing explosion protection measures in place at a site, operators must identify additional measures that are deemed necessary to further reduce the risk associated with explosion hazards. These measures should be included in an appropriately resourced implementation programme.
Hazardous area zoning
An important explosion protection measure specifically set out as a requirement in the legislation is the classification of those areas at a site 'in which an explosive atmosphere may occur in such quantities as to require special precautions to protect the health and safety of the workers concerned', into hazardous area zones.
The classification of different zones should be on the basis of the frequency and duration of the occurrence of an explosive atmosphere. The following zones are defined in the legislation:
- Zones 0, 1 & 2 for mixtures with air of flammable gases, vapours and mists.
- Zones 20, 21 & 22 for clouds of combustible dust in air.
Once zones have been identified, operators must install appropriate signage to identify them and must ensure that all mechanical and electrical equipment used within each zone is appropriate for use within that zone. All new equipment must be certified by the equipment manufacturer for use in the relevant zone.
There can be serious safety implications if an overly lax zoning philosophy is implemented at a site. On the other hand, there can be significant cost implications for operators who implement overly conservative hazardous area zones. Therefore, it is important that operators undertake realistic assessments of the type and extent of the hazardous area zones at their sites by carefully considering a variety of factors including the physical properties of the substance(s) released, the frequency and speed of the release, and the degree and availability of ventilation.
Various standards and codes of practice are available as guidance when undertaking hazardous area zoning.
Explosion protection document
The purpose of the explosion protection document (EPD) is to demonstrate compliance with different requirements of the ATEX legislation, including:
- Explosion hazard identification & risk assessment
- Hazardous area zoning
- Explosion protection measures
- Safe design, operation & maintenance of the workplace & work equipment
The EPD should be a concise, well-referenced, 'living' document and should be updated whenever there are relevant, significant changes at a site. The EPD must be made available to employees.
What should operators do next?
A useful first step is to undertake a gap analysis to identify the gap between the status quo at the site with respect to protection against explosive atmospheres and the requirements for full compliance with the ATEX legislation. This exercise should involve a rigorous comparison of the requirements set out in each of the key articles in the ATEX 'user' directive (as transposed into local legislation) and the relevant measures already in place at the site.
Byrne Ó Cléirigh's has extensive experience in undertaking risk management assignments at sites with explosive atmosphere hazards, including at pharmaceutical plants, chemical storage, oil storage & refining, LPG storage, solvent processing, metals processing, printing, packaging, brewing and powder handling facilities. Our ATEX services are described here.